CAT3 vs. CAT5 vs. CAT6
CAT3 vs. CAT5 vs. CAT5e vs. CAT6 vs. CAT6e vs. CAT6a vs. CAT7
While the consumer electronics keep going increasingly wireless, many LANs still rely heavily on CAT cables to handle all the heavy lifting when it comes to transmitting data. To begin with, all Ethernet cables are of two key varieties i.e. UTP (unshielded twisted pair) or STP (Shielded twisted pair) variety. They all have the same construction structure, but vary a great deal as far as transmission frequency and throughput are concerned. However, some terms need to be defined before any meaningful comparison can be presented:
How to interpret Ethernet cable Speed?
- 10 Mbps = 1.2 MB / s i.e. 1 hour to download a DVD (4.5 GB)
- 100 Mbps = 12 MB/s i.e. 1 hour to download 10 DVDs (assuming 4.5 GB average)
- 1.0 Gbps = 125 MB/s i.e. 1 hour to download 100 DVDs (assuming 4.5 GB average)
- 10 Gbps = 1.25 Gbps i.e. 1 hour to download 1000 DVDs (assuming 4.5 GB average)
What is Frequency?
Imagine you can only drive two cars, one passenger each, at a given time on a highway in each of the two lanes. Now you would be able to transfer more people over the same highway if you can drive the same two cars 500 trips per day compared to 250 trips per day.
Now imagine the same analogy but replace cars with bits of data. So if you can only drive two bits on a given data-line then 100 Mhz (or 100 million cycles per second) will give more bandwidth (i.e. ability to transfer data over the same line) then 50 Mhz (or 50 Million cycles per second).
UTP and STP Comparison Chart
CAT3
The Category 3 or CAT3 standard was used heavily in the early 90’s for wiring offices and homes. It’s still used in two-line phone configurations, but has largely fallen out of favor for wired networking thanks to the Category 5e cable’s superior performance. CAT3 can be relied on to handle data speeds of up to 10 Mbps, but no more. Its maximum frequency clocks in at 16 MHz. Like many other cabling options, it relies on copper for data and power transmission. While theoretically limited to 10BASE-T Ethernet, it can actually support 100BASE-T4 speeds by using 4 wires instead of 2 to achieve 100 Mbps throughput.
CAT5
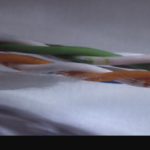
Around 2000 or so, CAT5 overtook CAT3 as the Ethernet cable of choice for LAN networking. CAT5 uses either the 10BASE-T or 100BASE-T standard for data transmission. Using two cable pairs to signal over copper wire, CAT5 is now largely archaic and isn’t widely used for Ethernet connections. It’s rated for a maximum frequency of 100 MHz and top speeds of 100 Mbps. CAT5 uses 8P8C modular connectors to connect devices together, and can be used effectively at lengths of up to 100 meters. Today, CAT5 cable has been replaced for the most part by CAT5e.
CAT5e
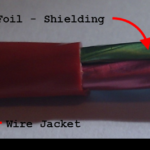
While very similar to CAT5 in appearance, CAT5e introduces some new wrinkles in the equation. For one thing, CAT5e uses four pairs of copper wire rather than the two that CAT5 relies on. In addition, the wire pairs are twisted more tightly and are sheathed in heavy-duty shielding to eliminate crosstalk. Crosstalk cuts down on the speed at which a cable can transmit information. Thanks to its internal upgrades, CAT5e is capable of achieving 1000BASE-T speeds. In other words, it can handle up to 1 Gbps of throughput at a distance of up to 100 meters. As of today, it’s the most common type of cabling found in modern homes and offices for Ethernet purposes.
CAT6
For back-end, high-capacity networking, CAT6 supports Gigabit Ethernet needs. Supporting frequencies of up to 250 MHz and the 10BASE-T, 100BASE-TX, 1000BASE-T, and 10GBASE-T standards, it can handle up to 10 Gbps in terms of throughput. Thanks to better cable insulation, CAT6 reduces potential crosstalk even more so than CAT5e. When used for Gigabit Ethernet and below, the maximum allowable cable length is 100 meters. For 10GBASE-T speeds, the maximum cable length is 55 meters. The one major caveat of CAT6 cables is that installation can be tricky, as compatibility with 8P8C requires the use of special adapter pieces for optimal performance.
CAT6e or Enhanced CAT6
These are an enhancement on the standard CAT6 cables, as they perform much better when installed in an environment with high noise or RF interference. While better than CAT6, they are not as good as the CAT6a or CAT6 Augmented standard cables.
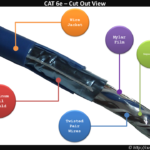
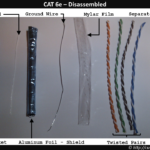
CAT6a
If you’re wiring up your home or office for Ethernet for the long haul, CAT6a is the perfect choice in terms of future-proofing. When it comes to A/V protocols, CAT6a is supposed to replace HDMI in the coming years. The main difference between CAT6a and CAT6 is that CAT6a can operate at a frequency of up to 750 MHz. In addition, CAT6a is even less susceptible to interference and crosstalk. The improved specification and shielding allows CAT6a to provide more consistently reliable speeds in difficult environments. Thanks to its performance and stability, CAT6a is the preferred cable for 10GBASE-T Ethernet.

Cat 7 and Beyond
The list of Ethernet options doesn’t stop at CAT6a. There’s also a version called CAT7 that’s even more capable than all of the TP cable variants listed above. CAT7, also known as Class F cable, supports transmission frequencies of up to 600 MHz. It supports 10GBASE-T Ethernet over a full 100 meters, and it features improved crosstalk noise reduction. While CAT6e is the current standard when it comes to 10GBASE-T, it will inevitably be replaced with CAT7. Nobody knows what the future holds for Ethernet cables or what will come next in terms of format or performance. No matter what happens, expect faster and faster cables with each passing year as the technology and protocols that support Ethernet continue to improve. Finally, one thing to always keep in mind is that any custom cable can be built to suit the application on any project.
Wired vs. Wireless Connections
Author’s note: While I have tried to keep any personal bias out of this post but it should still be read in the context of the idea that we would like to be preferred vendor for cable assembly and wire harness development and manufacturing.
The debate between using wireless or wired devices and networks often comes up in a few different contexts. Whether it is a personal Internet network for a home or in commercial applications like a wireless ECG/EKG monitor, technology has made it possible for numerous wireless items to reach the market. There are many business internet services out there, Primus is one example The question is whether wireless or wired options are better for the needs of the individual or company.
Comparison for Personal Use:

The use of a wireless router and a wireless system in a house or for personal devices like phones, MP3 players or similar portable electronics is a long-term trend. In personal use, wireless and wired options are often related to Internet usage. Both options, wired and wireless connectivity have their advantages and disadvantages that appeal on a personal level.
One of the first considerations is the level of convenience. In the case of convenience at home or on the road, wireless options are often the most convenient choice. Wireless networks can be accessed from any computer in the vicinity of the router, making it possible to connect several computers in one house. Another advantage is the ability to use wireless chargers and wireless devices while on the go. A wired connection is less versatile in personal use, so when it comes to convenience the wired options are at a disadvantage.
Security is another consideration with wired and wireless networking. In this category, wired networks are generally better because the security built into the system is better than a wireless option. Wireless will require taking some additional measures to secure the connection. That said, many wireless routers in the market today offer security settings at the click of a single button mounted on the front panel of the router or the switch. All too often, it would users own actions (visiting sites with malicious software and viruses, opening suspect emails, putting credit card information on unsecure webpages etc.) that will compromise their security before someone breaks through their WEP or WPA encryption.
Reliability is another feature to look for when determining whether to use wired or wireless connections. In the case of reliability, wired connections are generally best because interference is not an issue and speed remains steady as a result of the wire. With wireless networks one can casually walk in and out of the wireless’s range, often resulting in a dropped connection. Overall, the wireless connections do tend to be a little more fickle, often for reasons that the end user may never fully resolve.
Wired connections (@ 1000 mbps) remain at least three times faster than their wireless counter parts (@ 300 mbps) at least at the time of writing this article. Although this should have little to no impact on most end users since most residential broadband internet providers offer speeds well below the 300 mbps and at the same time, there is nothing stopping the end use from connecting their computers to the modem on as and when required basis.
In the area of personal use, wired devices have an advantage of being more secure and reliable than a wireless option. Unfortunately, in this area convenience will often outweigh the advantages of the wired options.
Comparison for Commercial Use:
While personal Internet usage and personal devices might use a wireless network, when it comes to commercial needs the determination of which system is better varies on different opinions and the needs of the products. Understanding the advantages and disadvantages of each system can make a difference between which system is better. In the case of commercial usage, or the use of commercial devices, the advantages and disadvantages might seem surprising.
One of the major considerations is the cost associated with a wire harness versus a wireless option. The wired device is infinitely less costly to develop and make, thus it is ultimately less costly to buy. When making commercial devices it is much less costly than putting together the components of a wireless system. The wired system has a clear advantage over the wireless when it comes to price, especially of the device is for a custom application and low volume.

Another consideration with wired and wireless commercial devices is the reliability. Since wireless will often have interference from other devices, the wired system is clearly superior in this instance. The design engineer or the developer would have one less variable to accommodate if they take the wired route. At the same time the designer can concentrate on the task at hand rather than spending time and resources on making a wireless system work, as well as meeting any regulatory requirements from independent bodies such as FCC. Commercial devices frequently require very reliability built into the system. The risk of losing the connection, or just degraded performance due to interference from external sources makes wireless options less advantageous.
As with any other system, wired connections are more secure than wireless options. In a commercial device, this security might make the difference between losing valuable data on the device or keeping it safe.
In commercial systems, a wired device is clearly superior to the wireless system because of the ease of product development; reliability; reasonable cost and security outweigh any minor convenience a wireless option might provide.
Comparison for Industrial Usage:
When considering whether to opt for wireless or wired solutions in an industrial setting, the factors are often different from personal usage or commercial usage. Using wired connectivity is sometimes the only available choice due to the fact that many industrial devices might not be economical to build and set up on a wireless interface.
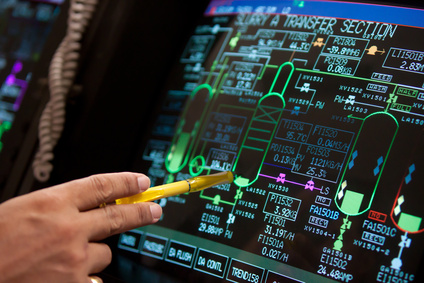
The first consideration related to industrial devices is the development cost of wireless. Industrial devices often require the use of custom cables and wire harnesses to allow the items to work effectively. In many cases, the cost of trying to develop a wireless system that will work integrate with the existing setup could be substantial. Often, there would lie more value in adding additional features in the same budget as opposed to making an effort on reliably and securely transmitting data over the wireless. Off course here the assumption is that any such system will need to transmit the data or I/O signals in real time; often attaching laptop to such a system and re-relaying the information over the wireless would make more financial sense.
The effectiveness of the equipment is another key point that industries must consider before looking into wireless options. As with any other system, a wireless device made for industries will have the limitations of any other electronic or similar item. The problem with this is the fact that the system might have interference that makes equipment stop working when it is on a wireless system. That can result in costly delays for a production line as then the line or system would be down or the data will be buffered all the while the cause of failure and a resolution is being determined.
Industries need reliable systems and many items like a programmable logic controller or current testers cannot afford the potential reliability problems that may be introduced with the wireless option. A PLC in particular is not worth creating as a wireless system because interference from common devices like cell phones might even put lives in danger as might happen if the PLC system at an amusement park suddenly lost the connection as there was one more variable for its proper operation.

Another factor that industries must consider is security. Poor security in a wireless system can be complicated to manage on the large scale of industrial equipment or computers. This can not only become expensive, but it can result in problems like viruses that ruin the system. A cable assembly is by design more secure, so the system is easier to keep from any security breaches.For industrial use, a wired system is a better option than trying to develop wireless options. The cost of traditional wire harness options, custom cable needs and cable assembly combined with the reliability and security makes a wired system the obvious choice for industries. Wireless is not an option when it can result in danger and potentially expensive delays.
The choice between wireless and wired systems is often a matter of using common sense and weighing the pros and cons. In a personal home or individual devices, a wireless system might be the most convenient and does not have the risks of commercial and industrial equipment and devices. For those looking at a commercial device or industrial systems, wired options are generally the better choice as a result of better safety and reliability. Lets not forget that some situations can be totally unique to a point that people will try any approach for a fast data transfer, as was the case with South African company that used a pigeon to send 4Gb over sixty miles.
Crimping Vs. Soldering For Cable Assemblies
Cable assemblies can be produced either with the aid of crimped connections or soldered connections. The type of desired connection type is merely a matter of choice. In general, the trade off is between speed and reliability. It is possible to achieve reliable connections in the least possible amount of time through soldering, yet it’s also possible to obtain connections that may be slightly more solid via soldering. Both mass production and custom production have preferred methods, and both of these connection styles have their strong points and their weaknesses.
Crimping vs Soldering For Cable Assembly
From a manufacturing perspective, the goal is throughput while maintaining quality. That almost definitely means that factory-made cable assemblies are produced with crimped connections. Making these connections is a simple as fitting the connector pins over the wires and using a reliably determined amount of force every time so that all pin connections are solid. The typical user will find that these crimped connections are secure enough for typical purposes. Cables for electronics purposes should never be placed under high tension or any other type of stress or strain. This might cause connections to come loose or wire insulation jackets to crack.
For those who need custom cables instead of the stock cable assemblies, whether to use crimped or soldered connections is simply a matter of choice. The reason soldered connections typically are not used in production environments is because of the time it takes to make each connection. Soldering requires heating the two metal surfaces to be mated so that the solder melts. This process requires special attention to detail. During the soldering process the wire insulation jacket should not become so hot that some of it melts and becomes trapped between the individual strands of wire. Also, concluding the soldering process, the solder flux has to be cooked out of the connection to ensure a reliable connection. For those who are proficient in their soldering skills, reliable connections can be achieved that are just as good as or even better than the crimped connections.
Soldering may also be an attractive option for those who only wish to produce a small quantity custom cables. Depending upon the type of connection, some of these crimping tools can cost nearly as much as the cable if not more. A soldering iron can be used for numerous projects, which brings down the cost of this job and many others, depending upon the life of the iron and the number of tasks. The decision whether to use crimped connections or soldered connections does not make a significant difference with regard to the useful life of the cable.

From the standpoint of longevity, either type of connection should last for the life of the user. However, given that most wires are made from copper, the soldered connection might provide slightly better protection against the corrosion that occurs just from normal open air exposure. Realistically, any resulting corrosion is slight, usually amounting no more to a native layer of oxidation. From a process perspective, crimping will always be preferred as the number of controllable variables are significantly less than soldering.
The terminals are standardized and will accept either type of connection. Whether these are custom cables or standard factory made cables, they should connect the same. From the standpoint of making connections to the terminals there is no significant difference. Using one type of connection over the other is merely a choice to be made at the discretion of the user. Crimped connections can be faster to produce, though soldered connections may provide a slightly more solid connection. Since both are equally capable of performing the same function, the real concern should be for the individual cable wires. These wires should be protected against stresses and strains that may cause the insulation jacket to weaken and even break.